plant buddy
This is my final year project in SUTD, where my team and I collaborated with mentors from Panasonic. The aim was to develop a consumer product to educate and engage children in urban farming, exposing them to sustainability and food security.
​
My role as the hardware design engineer was to transform user needs into a manufacturable, functional and safe hardware product.
​
Skills: DFMA, CAD, UX
​
Check out our project page for a fuller scope:
https://capstone2021.sutd.edu.sg/projects/plant-buddy
​
(Update) Sep '21: Our project was featured on Channel 8!
Check it out:
https://www.youtube.com/watch?v=imI9kSUTEMA
​
This is the most hardcore, yet lovable, team ever ↓

Reality Check 1: Conflicting design modalities can help
It became apparent very early on that a hardware pot designed to be injection-moulded will not be optimised for 3D-printing, and vice-versa.
​
As such, two versions of the hardware pot were created in tandem: One that was optimised for additive manufacturing, and another that was designed to be injection-moulded. The former allowed prototyping to be truly rapid enough to keep pace with internal testing, and the latter would be for mass manufacturing by Panasonic.
While time-consuming, this approach proved to be helpful for the team to conduct user testing uninterrupted while production was underway. In fact, by the time the parts arrived, our team had already incorporated several new design changes.
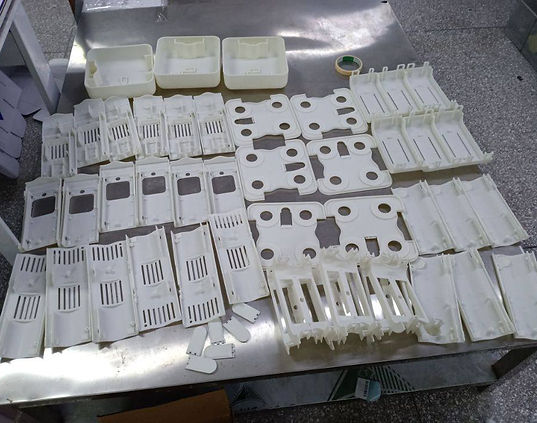
Parts manufactured by our overseas vendor that truly saved us
Reality Check 2: Designing for children is different
As much we wanted to believe that we could predict and project the psyche of children, we knew that the design process would be incomplete if we did not have a close working relationship with the end-users themselves.
​
As such, our team conducted several rounds of user testing at various stages of development. We started with an exploratory session in small groups with children of friends and family. We used paper prototypes for both the hardware and the software to try and extract the pain points and user needs.
After developing new hardware and software features from the insights gathered, we continued to engage the same set of children in two more follow-up sessions. The engagement with these children gave us a firsthand look at how a potential end-user will interact with and learn from our product.
Despite scheduling hurdles (causing us to 'work' on weekends and public holidays), this approach gave us immediate and reliable feedback. The qualitative data that we picked up from the children and their parents gave our team a clear design direction at every step of the way.

Snippet from one of our earlier user testing sessions
Reality Check 3: Post-processing is magic
Extensive post-processing of parts printed using FDM-based printers can rival the finishing of injection-moulded parts (at least to the untrained touch) - tried and tested. I was genuinely surprised.
​
Also when used well, soluble supports can drastically improve print quality and cut down on post-processing time.

Me, removing soluble supports from our PolyJet print
Overarching Takeaways
-
Taking assembly into consideration when designing a product is just as important of manufacturability. It could make the difference between fuss-free maintenance and a practically unserviceable product.
-
Designing for a specific target audience can be a tricky balancing act where we must avoid over-generalising the opinions of a small group of users. Nonetheless, it is extremely fulfilling to develop a product alongside the target users - children, in our case.
-
The interface between a hardware product and an accompanying mobile app is a tricky one to get right. Hence, frequent sharing between the hardware and software teams is critical.

Plant Buddy